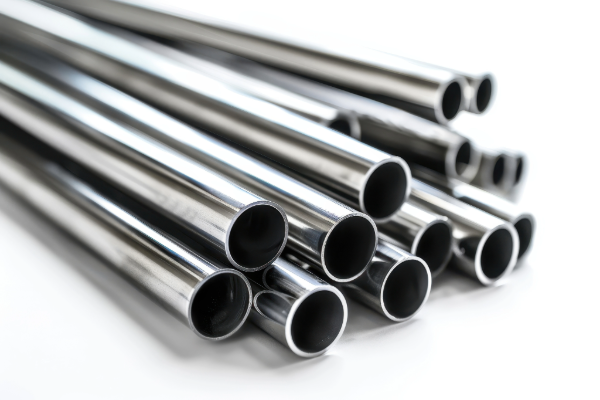
The design of a solenoid valve requires the use of different materials. The valve body is often made of metals such as brass, aluminum or stainless steel. For sealing, flat gaskets, O-rings or similar, made of elastomers or for example PTFE, are used. The solenoid coil consists of enameled copper wires that are pressed around with a plastic. In addition to other parts, the pole and the plunger of the solenoid valve play a central role. These are almost always made of ferritic stainless steels with the property of being magnetizable, in contrast to austenitic stainless steels, which are used for the valve body or for springs, for example.
The most commonly used ferritic stainless steel for magnetic cores or poles is material number 1.4105. In applications with aggressive media, this material is sometimes the weakest link in the chain of materials used, which can lead to corrosion problems.
A very good material in terms of its magnetic properties would be technical iron. However, as this does not have sufficient corrosion resistance, it must be processed with other elements to form an alloy. In addition to the main alloying elements iron and chromium, stainless steels contain silicon, manganese and carbon. It can also contain molybdenum, which increases corrosion resistance, and sulphur, which improves machinability.
Although a high alloy content can lead to excellent corrosion resistance, there are generally fewer iron atoms available, which contribute to magnetic saturation.
The alloy must therefore be selected with both good magnetic properties and sufficient corrosion resistance in mind.
In addition to the material 1.4105, the materials 1.4106 and 1.4113 are also available, for example, which have a slightly higher corrosion resistance, as shown by the salt spray test (in hours) in the following table as a measure of corrosion resistance. Due to a higher proportion of molybdenum, 1.4106 and 1.4113 have a higher corrosion resistance than 1.4105. 1.4113 is even more resistant than 1.4106, as 1.4106 is additionally alloyed with sulphur, which has a positive influence on the machinability of the material, but a negative influence on the rust resistance.
Material | Composition | Salt spray test (h) | Rel. permeability (μr)r) |
1.4105 | X6CrMoS17 | <500 | 1500-2000 |
1.4106 | X2CrMoSiS18-2-1 | 300-700 | 1500-2000 |
1.4113 | X6CrMo17-1 | 700-1000 | 1500-2000 |
