Conventional solenoid valves are generally used to switch gas and liquid flows and thus only perform the states "On" and "Off". In order to not only switch but also control mass flows, proportional valves are used to control the opening degree of the valve and thus the mass flow.
Switching valves (solenoid valves) and proportional valves often differ only minimally from each other in terms of their external appearance and internal structure. The reason for this is that the poppet valve design is well established and tested and can be implemented cost-effectively. Many components, such as the body of the solenoid valve, can be used unchanged for both solenoid valves and proportional valves.
The difference between the two valves usually is in details, namely in the design of the plunger or the pole as a counterpart to the plunger. Solenoid valves have a flat pole and a movable plunger without a special shape. In the characteristic curve of the solenoid valve, this geometry has the effect that the force that presses the movable plunger against the pole increases quadratically as the air gap δ becomes smaller (images in the left-hand column). By shaping the plunger or pole more elaborately, as indicated in the figure below, the course of this characteristic curve can be changed in a targeted manner. This allows, for example, a linear force curve to be generated over a wide range δ. Such optimizations can be used to create a relationship between the flow through the solenoid valve and the duty cycle of the pulse-width modulated supply voltage that is as linear as possible, as is intended for proportional valves.
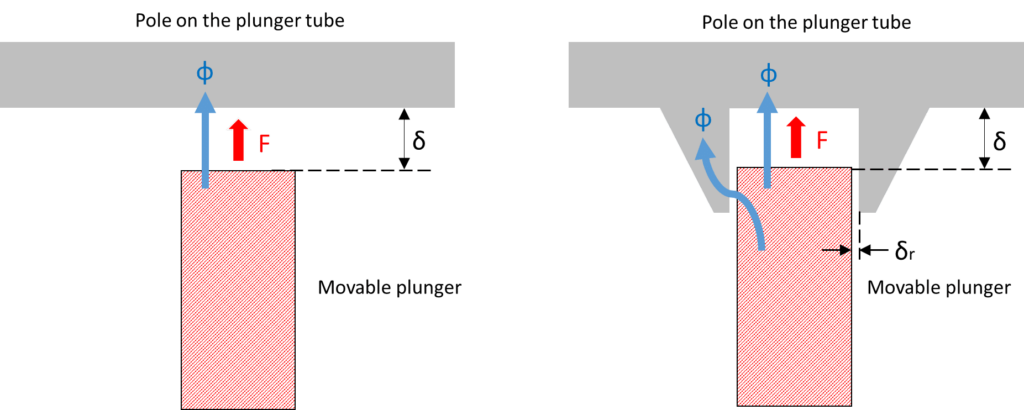
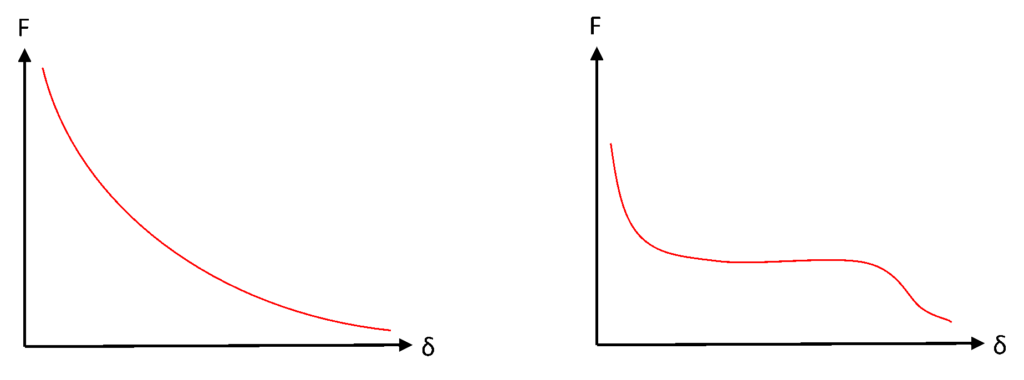