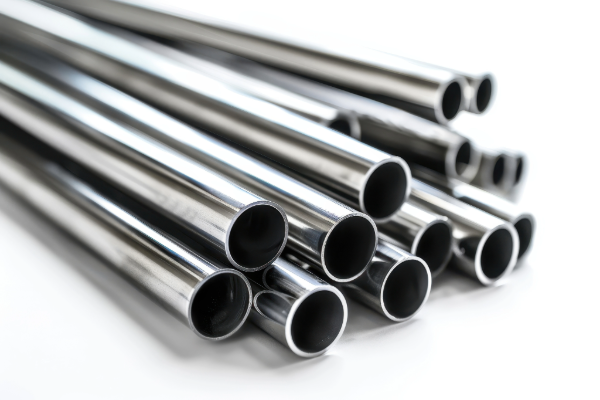
Der Aufbau eines Magnetventils erfordert den Einsatz unterschiedlicher Materialien. Der Ventilkörper besteht häufig aus Metallen wie Messing, Aluminium oder Edelstahl. Zum Abdichten werden Flachdichtungen, O-Ringe oder ähnliches verwendet, die aus Elastomeren oder z.B. PTFE bestehen. Die Magnetspule besteht aus lackierten Kupferdrähten, die mit einem Kunststoff umpresst werden. Neben weiteren Teilen nehmen der Pol und der Magnetkern des Magnetventils eine zentrale Rolle ein. Diese bestehen so gut wie immer aus ferritischen Edelstählen mit der Eigenschaft, dass diese im Gegensatz zu den austenitischen Edelstählen, die z.B. für den Ventilkörper oder für Federn eingesetzt werden, magnetisierbar sind.
Der am häufigsten eingesetzte ferritische Edelstahl für Magnetkerne oder Pole ist die Werkstoffnummer 1.4105. In Anwendungen mit aggressiven Medien ist dieser Werkstoff gelegentlich das schwächste Glied in der Kette der eingesetzten Materialien, wodurch Korrosionsprobleme auftreten können.
Ein sehr gutes Material, gemessen an seinen magnetischen Eigenschaften, wäre technisches Eisen. Da dieses jedoch keine ausreichende Korrosionsbeständigkeit hat, muss es mit weiteren Elementen zu einer Legierung verarbeitet werden. Neben den Hauptlegierungselementen Eisen und Chrom enthalten rostfreie Edelstähle Silizium, Mangan und Kohlenstoff. Ferner kann auch Molybdän enthalten sein, welches die Korrosionsbeständigkeit erhöht, und Schwefel, welcher zur Verbesserung der Spanbarkeit führt.
Ein hoher Legierungsanteil kann zwar zu einer ausgezeichneten Korrosionsbeständigkeit führen, in der Regel stehen dann aber auch weniger Eisenatome zur Verfügung, die zur magnetischen Sättigung beitragen.
Die Auswahl der Legierung muss daher unter beiden Gesichtspunkten, guten magnetischen Eigenschaften und einer ausreichenden Korrosionsbeständigkeit, erfolgen.
Neben dem Werkstoff 1.4105 stehen dazu z.B. noch die Werkstoffe 1.4106 und 1.4113 zur Verfügung, welche über eine etwas höhere Korrosionsbeständigkeit verfügen, wie die Angabe des Salzsprühnebeltests (in Std.) in der folgenden Tabelle als Maß für die Korrosionsbeständigkeit zeigt. Durch einen höheren Anteil von Molybdän weisen 1.4106 und 1.4113 eine höhere Korrosionsbeständigkeit auf als 1.4105. 1.4113 ist gegenüber 1.4106 noch beständiger, da 1.4106 zusätzlich mit Schwefel legiert ist, was einen positiven Einfluss auf die Spanbarkeit des Materials hat, jedoch einen negativen Einfluss auf die Rostbeständigkeit.
Material | Zusammensetzung | Salzsprühnebeltest (h) | Rel. Permeabilität (μr) |
1.4105 | X6CrMoS17 | <500 | 1500-2000 |
1.4106 | X2CrMoSiS18-2-1 | 300-700 | 1500-2000 |
1.4113 | X6CrMo17-1 | 700-1000 | 1500-2000 |
